广州有色金属非金属夹杂物检验
金属物理性能检测的方法有很多种,常见的方法包括以下几种:1、硬度测试:常见的硬度测试方法包括布氏硬度、洛氏硬度和维氏硬度等。2、强度测试:金属强度主要包括屈服强度、抗拉强度、剪切强度和压缩强度等,测试方法包括拉伸试验、压缩试验、弯曲试验和剪切试验等。3、导电性测试:导电性测试方法包括四线法、哈特曼法和电容式法等。4、导热性测试:测试方法包括横向法、纵向法和稳态法等。5、磁性检测:磁性检测方法有磁通法、差动法和电磁超声法等。6、显微结构检测:常见的显微结构检测方法包括光学显微镜、电子显微镜和扫描电子显微镜等。金属锻件物理性能检测的方法主要包括力学性能测试、金相组织分析、硬度测试和冲击试验等。广州有色金属非金属夹杂物检验
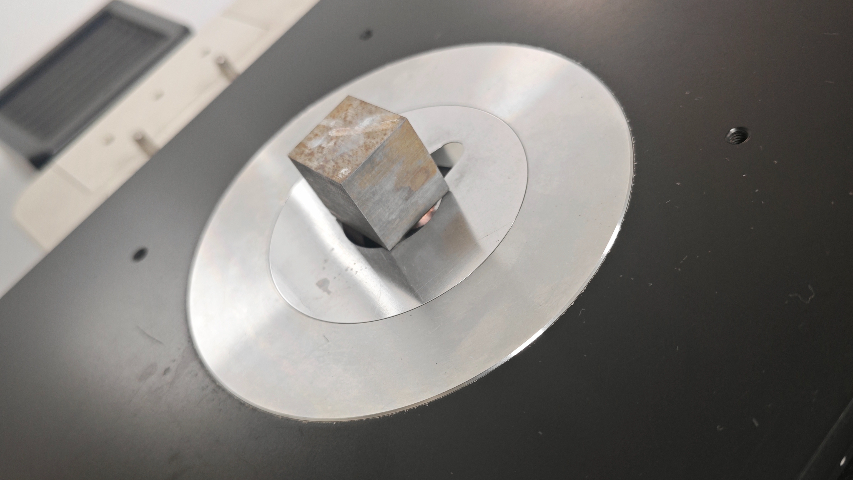
金属低倍组织检验需要准备哪些试样?金属低倍组织检验需要准备的试样包括:1、金属标本:金属标本是进行低倍组织检验的基础。通常情况下,金属标本是从被检测物体中取出的小块金属,经过磨削、打磨、抛光等处理后制成。2、研磨纸:研磨纸是用来磨削金属标本表面的工具。常用的研磨纸有各种粗细不同的砂纸、研磨布等。3、研磨液:研磨液是用来润滑研磨纸的液体。通常使用的研磨液有水、乙醇、甲醇等。4、腐蚀剂:腐蚀剂是用来腐蚀金属标本表面的试剂。常用的腐蚀剂有酸、碱等。5、显微镜:显微镜是用来观察金属标本组织结构的仪器。常用的显微镜有光学显微镜、电子显微镜等。有色金属低倍组织检验怎么样金属金相检验是通过对金属材料微观结构的分析和评估,来确认材料的质量、结构和性能的一种方法。

金属低倍组织检验中,晶粒大小对材料性能有何影响?1、机械性能差:晶粒较大时,材料的强度、韧性和延展性等机械性能会降低。这是因为一个晶粒内部存在较多的晶界和微缺陷,这些缺陷易于成为断裂的起点,从而降低材料的断裂强度和延展性。2、耐蚀性差:晶粒较大时,材料的耐蚀性也会变差。晶界是材料中腐蚀的敏感区域,晶粒较大时,晶界的比例也会增加,从而导致材料的耐蚀性变差。3、信号差:晶粒较大时,材料中的组织结构不规则,信号的传递也会受到阻碍。对于一些特殊的材料,例如电子器件中使用的半导体材料,晶粒大小对信号的传递和响应也有着重要的影响。
金属低倍组织检验中,如何判断材料在加工过程中是否发生了变形?在金属低倍组织检验中,判断材料在加工过程中是否发生了变形,可以从以下几个方面进行观察和分析:1、观察晶粒形状和大小:如果材料的晶粒形状和大小不均匀,或者出现了明显的拉伸、扭曲等变形,那么就可以判断材料在加工过程中发生了变形。2、观察晶界和相界:如果材料的晶界和相界出现了明显的拉伸、扭曲等变形,那么也可以判断材料在加工过程中发生了变形。3、观察组织中的夹杂物和缺陷:如果材料中出现了明显的夹杂物和缺陷,特别是沿着加工方向分布的夹杂物和缺陷,那么也可以判断材料在加工过程中发生了变形。4、观察材料的硬度和强度:如果材料的硬度和强度与原材料相比有明显的提高,那么也可以判断材料在加工过程中发生了变形。金相检验是一种通过显微镜观察金属材料的组织结构来评估其性能和质量的方法。

金属晶粒度检验中使用的试样应该有什么特点?1、试样的制备应该规范、标准化,以确保数据的准确性和可靠性。2、试样应该象征整个金属材料的微观组织特征,因此应该从不同的位置和方向采集试样,并在不同的部位进行测量。3、试样应该平面,不应该有凸起或凹陷,以避免影响测量结果。4、试样应该不含任何杂质或异物,以避免对结果的影响。5、试样的表面应该光滑,没有明显的磨损或瑕疵,以确保测量的精确性。6、对于某些需要在高温环境下进行检验的材料,试样应该可承受高温,而且应该选用合适的材质来保证试样的稳定性和准确性。金属材料金相检验是一种通过显微镜观察金属组织结构来评估材料性能的方法。湖州金属棒材晶粒度检验服务厂商
黑色金属低倍组织检验是一种常用的物理性能检测方法。广州有色金属非金属夹杂物检验
金属物理性能检测是一种对金属材料进行测试和分析的过程,以确定其物理性能和机械性能。这些测试可以包括硬度、延展性、强度、韧性、耐磨性和抗腐蚀性等方面的测试。在金属金相检验中,不同材料的显微组织和异常可以通过显微镜观察来判断。这些异常包括晶粒大小、晶界、裂纹、夹杂物等,这些都可以影响材料的性能和使用寿命。通过对这些异常的检测和分析,可以确定材料的质量和可靠性,以及材料是否符合所需的技术规范和标准。金属金相检验通常用于评估金属材料的质量和可靠性,以及确定材料是否符合所需的技术规范和标准。这些检验通常在生产过程中进行,以确保生产的金属材料符合质量标准。此外,金属金相检验还可以用于研究和开发新的金属材料,以及评估现有材料的性能和可靠性。广州有色金属非金属夹杂物检验
上一篇: 广州金属型材物理性能检测
下一篇: 广州金属锻件金相检验